Hydraulic systems are the lifeblood of numerous industries, powering machinery used in construction, manufacturing, agriculture, and more.
The efficiency, longevity, and performance of these systems depend heavily on one critical factor: the right hydraulic lubrication oil. Choosing the correct oil isn’t just a matter of maintenance; it’s a strategy to maximize performance, minimize downtime, and protect your investment.
In this blog, we’ll dive deep into the factors to consider when selecting hydraulic lubrication oil, its importance, and tips for ensuring your hydraulic systems deliver maximum performance.
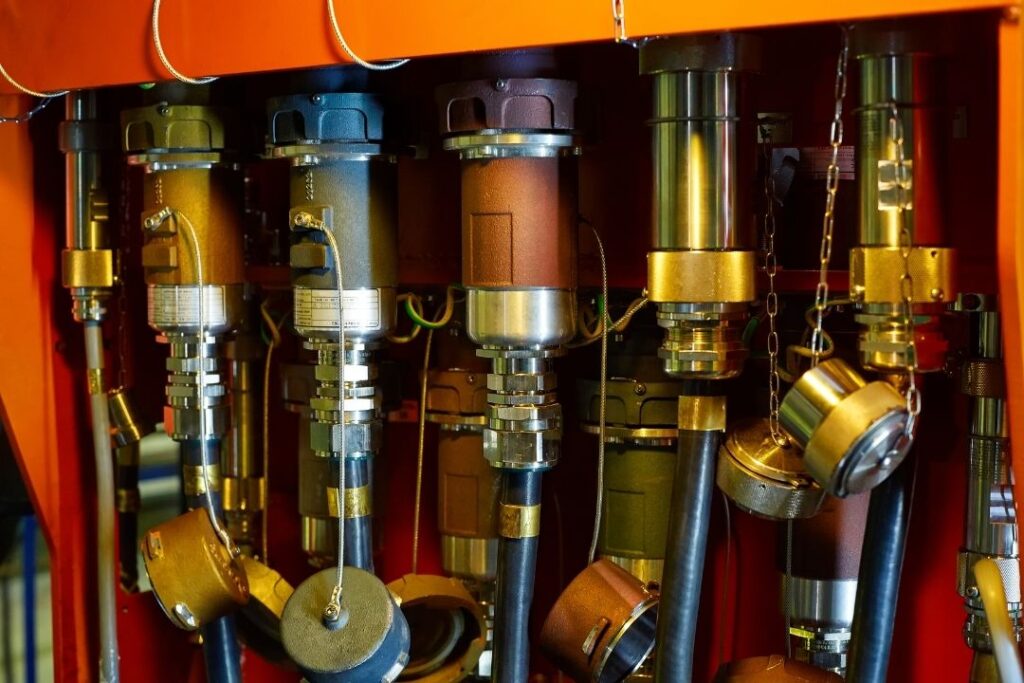
What Is Hydraulic Lubrication Oil?
Hydraulic lubrication oil serves dual purposes: it transmits power within the hydraulic system and lubricates its moving parts.
This oil ensures the smooth operation of hydraulic pumps, valves, cylinders, and other components, while also protecting them from wear, corrosion, and overheating.
The right hydraulic oil must meet specific operational demands, such as high pressure, varying temperatures, and the presence of contaminants, all while maintaining its viscosity and protective properties.
Why Is Choosing the Right Hydraulic Oil Important?
- Performance Optimization: Hydraulic oil directly influences system efficiency. The right oil ensures consistent power transmission, reducing energy losses.
- Component Protection: Proper lubrication minimizes wear, preventing costly breakdowns and extending component life.
- Thermal Stability: High-quality hydraulic oil maintains its properties under extreme temperatures, reducing the risk of overheating or system failure.
- Contamination Control: Specialized additives help hydraulic oil resist degradation from contaminants like dirt, water, and air.
- Cost Savings: The right oil reduces maintenance needs, downtime, and repair costs, delivering long-term savings.
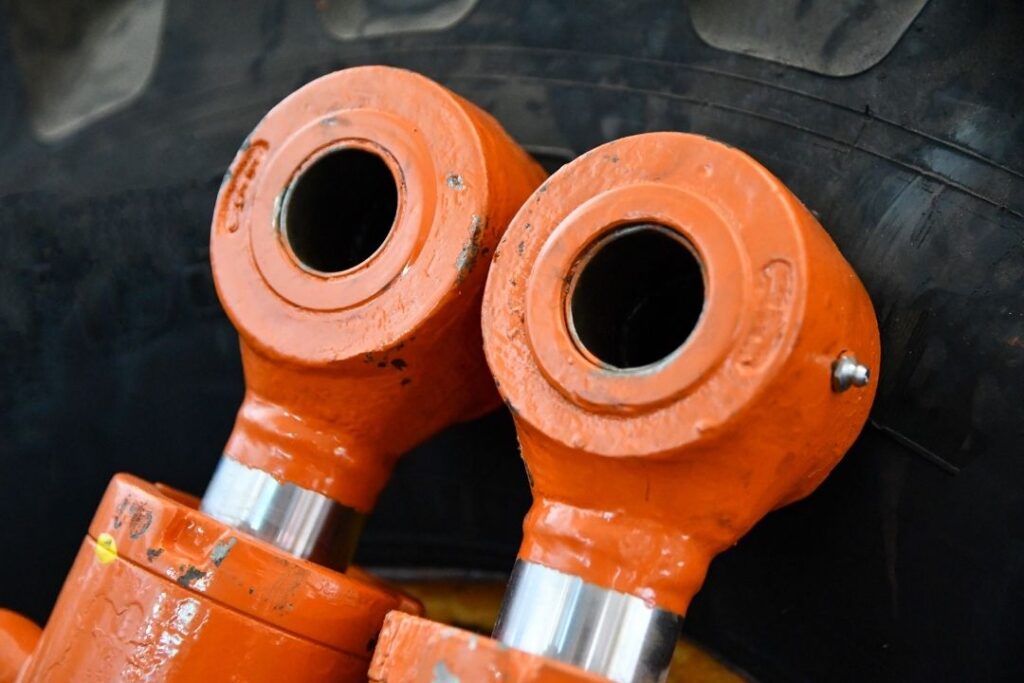
Factors to Consider When Choosing Hydraulic Lubrication Oil
1. Viscosity Grade
Viscosity, or the oil’s thickness, is a critical factor. Hydraulic oils are classified into different grades based on their flow characteristics under specific conditions.
A mismatch in viscosity can lead to poor lubrication, overheating, or sluggish system performance.
Tips:
- Consult the manufacturer’s manual for recommended viscosity grades.
- Consider operating temperature ranges, as oil thickens in cold conditions and thins in heat.
2. Additive Package
Hydraulic oils often contain additives to enhance performance. Look for oils with:
- Anti-wear additives: Protect components from friction and wear.
- Corrosion inhibitors: Prevent rust and oxidation.
- Foam suppressants: Reduce foam formation for consistent power transmission.
- Detergents: Keep the system clean by suspending contaminants.
3. Thermal and Oxidation Stability
Hydraulic systems often operate under high pressures and temperatures. Oils with poor thermal or oxidation stability can degrade quickly, forming sludge and deposits. Choose oils designed to withstand your system’s operating conditions.
4. Compatibility
Ensure the oil is compatible with your system’s seals, hoses, and materials. Incompatible oil can cause seal swelling, leakage, or degradation.
5. Environmental Considerations
For systems operating in environmentally sensitive areas, look for biodegradable hydraulic oils. These eco-friendly options minimize environmental impact in case of leaks or spills.
6. ISO Standards and Certifications
Hydraulic oils should meet industry standards, such as ISO 11158 or DIN 51524. Certifications indicate that the oil meets performance and safety benchmarks.
Types of Hydraulic Oils
- Mineral-based Oils:
Derived from refined crude oil, these are the most common and cost-effective. They are suitable for standard hydraulic systems with moderate operating conditions. - Synthetic Oils:
These oils are engineered for superior performance in extreme conditions, such as high temperatures or pressures. While more expensive, they offer longer service life and better stability. - Water-based Fluids:
Used in fire-resistant applications, water-based hydraulic oils have low flammability but may require additional care to prevent corrosion. - Biodegradable Oils:
Ideal for environmentally sensitive applications, these oils decompose naturally, reducing ecological risks.
Top Tips for Hydraulic Oil Maintenance
- Regular Oil Analysis: Periodic testing helps monitor oil condition and detect contamination, wear metals, or degradation.
- Filter Maintenance: Clean or replace filters to ensure contaminants don’t circulate in the system.
- Monitor Operating Conditions: Avoid exceeding temperature, pressure, or load limits to prolong oil life.
- Proper Storage: Store hydraulic oil in sealed, clean containers away from moisture and dirt.
- Follow Manufacturer Guidelines: Always adhere to the equipment manufacturer’s recommendations for oil selection and maintenance schedules.
Signs You’re Using the Wrong Hydraulic Oil
Using unsuitable hydraulic oil can lead to noticeable issues, such as:
- Increased noise levels or vibrations.
- Overheating or excessive energy consumption.
- Leaking seals or damaged components.
- Reduced equipment efficiency or sluggish operation.
If you observe these symptoms, assess your hydraulic oil and consult a professional for advice.
To Sum It Up
Selecting the right hydraulic lubrication oil is not just about meeting operational requirements—it’s about ensuring your hydraulic system delivers peak performance, efficiency, and reliability.
By understanding your system’s needs, consulting manufacturer guidelines, and choosing oil with the appropriate properties, you can maximize productivity and reduce operational costs.
Invest in quality hydraulic oil, maintain your system diligently, and you’ll enjoy the benefits of a robust and efficient hydraulic system for years to come.
FAQ’s
1. What happens if I use the wrong hydraulic oil?
Using the wrong hydraulic oil can lead to overheating, increased wear on components, system inefficiencies, and even equipment failure. It’s essential to follow the manufacturer’s recommendations for the best results.
2. How often should I change hydraulic oil?
The oil change interval depends on factors like the type of oil, operating conditions, and manufacturer guidelines. Regularly perform oil analysis to determine when a change is needed, typically ranging from 1,000 to 5,000 hours of operation.
3. Can I mix different hydraulic oils?
Mixing hydraulic oils is generally not recommended, as it can lead to compatibility issues, such as additive separation or reduced performance. Always ensure the oils are compatible if mixing is unavoidable.
4. What’s the difference between mineral and synthetic hydraulic oils?
Mineral oils are derived from refined crude oil and are suitable for standard applications, while synthetic oils are engineered for extreme conditions and offer better thermal stability, oxidation resistance, and longevity.
5. How can I tell if my hydraulic oil is contaminated?
Common signs of contamination include cloudy oil, a burnt smell, excessive noise in the system, and erratic machine performance. Regular oil analysis can identify contaminants early and prevent system damage.