Machining with carbide tools is one of the most common practices in the manufacturing industry, since it can be used at high speeds, remains sharp, and has excellent wear resistance.
Since carbide boasts a high level of hot hardness, tools made from this material require effective cooling during machining.
Soluble oil in plant coolants is commonly used for this purpose due to its superior cooling properties and excellent lubrication. This is achieved through the blending of oil and water, ensuring optimal performance and protection for carbide tools.
However, just like in any machining process, the right coolant is critical to achieve maximum tool life, good part quality, and effective operation.
Why Coolants are essential in Carbide Machining
During machining, especially with carbide tools, much heat is generated because of the high speeds and forces involved. High temperatures can cause tool wear, dimensional inaccuracies, and poor surface finish. Coolants are essential in:
- Heat Transfer: Coolants transfer heat away from the cutting zone, preventing overheating of both the tool and the workpiece.
- Lubrication: They reduce friction between the cutting tool and the work, increasing tool life as well as machining efficiency.
- Chip evacuation: Adequate coolant flow flushes the chips, thereby preventing them from interfering with the machining process.
- Surface finish: Coolants help in obtaining better surface finishes because the coolant reduces the flank wear of the tool and maintains constant conditions for cutting.
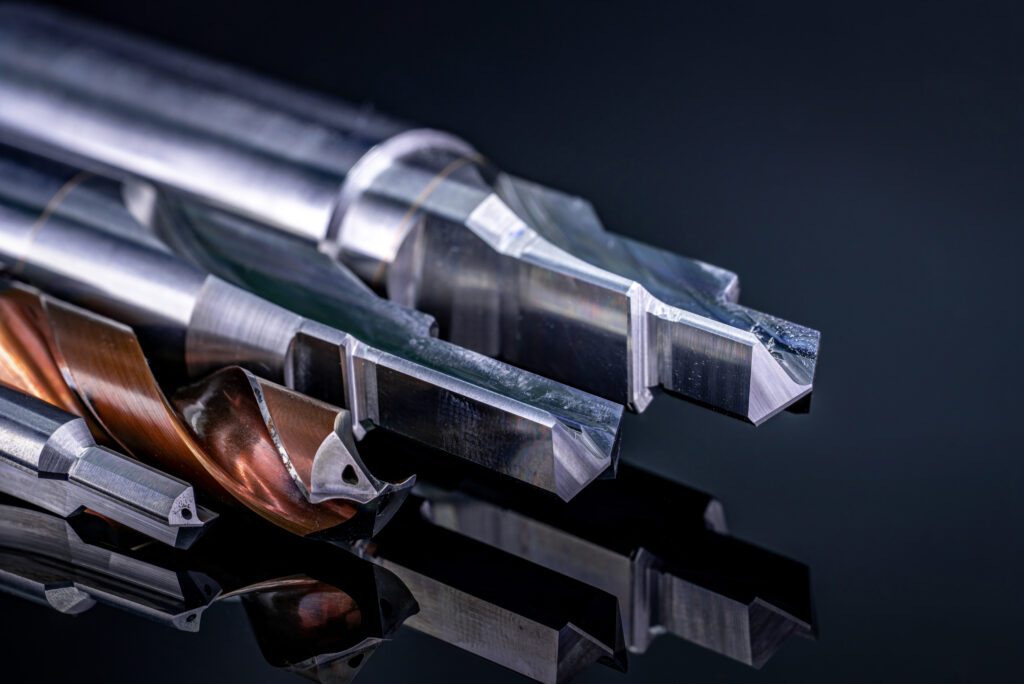
Understanding Carbide Tools
These tools are the carbide type- cutting tools that have a composite composition, primarily there is tungsten carbide, and as a binder, cobalt. Known for high durability, this tool doesn’t soften even in high-temperature operations and has a high speed of the cutting process.
It has the additional advantage of high precision, which is useful in achieving fine tolerances in manufacturing processes. Aerospace, automotive, and metalworking industries highly rely on carbide tools to assure performance and accuracy.
Types of Coolants Used in Carbide Machining
- Water soluble Coolants
Water-miscible coolants are used in several machining operations that require the use of carbide tools. Water-miscible coolants are aqueous solutions of oil-based or synthetic fluids.
Their water component gives excellent cooling since it contains such a huge heat capacity, and their oil component gives lubricity.
Some benefits include- excellent dissipation of heat, lower cost and nontoxic materials. These coolants could be formulated with additives in case of specific requirements, which include rust inhibitors or biocides.
- Synthetic Coolants
Synthetic coolants are made of chemical compounds without any petroleum oils. They give better cooling and are quite effective in high-speed machining operations where the heat generation is high.
Synthetic coolants offer a better cooling performance and provide less bacterial growth, less residue buildup, keeps the machine and parts clean.
- Semi-Synthetic Coolants
These are a mix of both soluble oils and synthetics as they contain oil as well as synthetic components. Semi-synthetic coolants are not only good coolants but also excellent lubricants. Thereby, semi-synthetic coolants can be used in a variety of machining operations.
Semi-synthetics give off less oil mist and smoke than straight oils.
- Straight Oils
Straight oils, or neat oils, are non-water-miscible coolants made of 100% petroleum or mineral oils. These coolants offer excellent lubrication but less effective cooling characteristics compared to water-based coolants.
Straight oils are often used in low-speed or heavy-duty machining operations where lubrication is very important; however, its use with carbide tools in high-speed operations is limited due to its poor cooling characteristics.
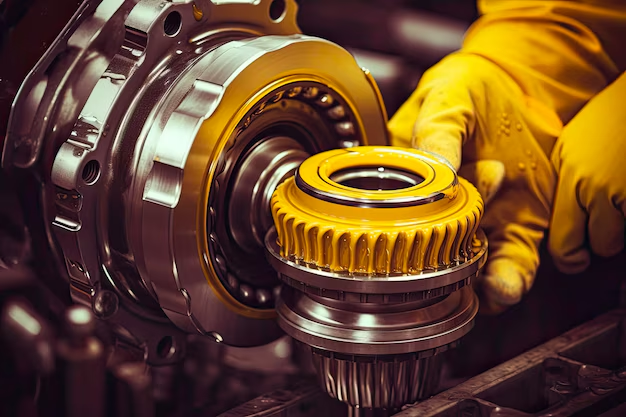
Factors to consider while choosing a coolant
When selecting the right coolant for machining, several critical factors must be considered to ensure optimal performance, tool longevity, and safety.
- Material
Different materials react uniquely to various coolants; for example, harder metals like titanium or stainless steel may require coolants with superior heat dissipation properties, while softer metals like aluminum might need a coolant that prevents buildup and galling.
Matching the coolant to the material helps in achieving smoother cuts and prolongs the life of both the tool and the workpiece.
- Type of operation
Operations such as turning, milling, drilling, or grinding have distinct demands. High-speed operations like drilling and milling generate more heat, requiring coolants with excellent thermal conductivity to dissipate heat effectively.
On the other hand, slower processes or those that involve complex geometries, such as threading or deep-hole drilling, might prioritize lubrication to reduce tool wear and improve surface finish.
Understanding the specific needs of each operation ensures that the chosen coolant enhances performance rather than hinders it.
- Machine speed and temperature considerations
High-speed machining can cause significant heat buildup, which, if not managed properly, can lead to thermal expansion of the workpiece, dimensional inaccuracies, and even tool failure.
Coolants with high cooling capacity are essential in these scenarios to maintain temperature stability.
Additionally, some coolants are designed to perform better under extreme temperatures, maintaining their effectiveness without breaking down. The choice of coolant should align with the operational parameters of the machine to avoid any compromise in productivity or quality.
- Environmental and safety considerations
Modern machining environments are increasingly focused on sustainability and worker safety.
Choosing coolants that are biodegradable, non-toxic, and free from harmful chemicals like chlorine and sulfur helps in reducing the environmental impact and adhering to regulatory standards.
Furthermore, coolants that are less prone to bacterial growth and have low misting properties contribute to a healthier work environment by minimizing exposure to harmful fumes or aerosols.
Proper disposal and recycling of used coolant are also important, as mishandling can lead to environmental hazards.
A well-chosen coolant not only enhances machining efficiency and tool life but also supports a safer and more sustainable manufacturing process. By aligning the coolant’s properties with the specific demands of the task, manufacturers can achieve better performance, cost savings, and compliance with environmental regulations.
Best Practices when Using Coolant with Carbide Tools
- Select the appropriate coolant
Select a coolant based on the specific machining operation, material, and tool requirements. For high-speed machining with carbide tools, water-soluble or synthetic coolants are typically preferred because of their excellent cooling ability.
- Maintain the correct concentration
Always mix the coolant to the manufacturer recommended strength; low concentration dilutes the oil film and offers only poor protection against corrosion, and too rich an engine will not cool enough.
- Maintain adequate flow
Sufficient flow is essential to effectively remove chips and heat generated in a cutting operation; this must be combined with proper filtration and maintenance so as not to clog up in delivery systems, thus impairing flow.
- Regular Monitoring and Maintenance
Monitor the coolant condition regularly in terms of pH levels, concentration, and contamination. There should be a scheduled replacement or replenishment of coolant whenever necessary to ensure its effectiveness.
How to choose the best coolant for carbide tools
To select the optimized coolant for carbide tools, one has to take into consideration various aspects such as the machining requirements, materials’ properties, and the particular objectives set for operations and cutting tools lives.
Also, the selection of the coolant should take into account compatibility with the materials being machined, for example, a coolant should be inert to the cutting tool made of carbide as well as the workpiece material.
That’s what makes Lubeco Green Fluids the perfect choice- no matter what your needs in terms of carbide tools and metalworking, our extensive range of Lubeco coolants and cutting fluids is guaranteed to include the perfect product.
From water-soluble and oil-soluble lubricants, to speciality metalworking fluids, Lubeco Green Fluids provides the ideal solution for any and all requirements.
Summing it up
Optimizing the choice of coolants in machining with carbide tools ensures optimum performance, long tool life, and good finish. It is essential to choose the best coolant as the preferred type is either water-soluble or synthetic coolant that has an excellent cooling capability.
The best practices regarding selection, application, and maintenance of coolants are applied to enhance machining operations in terms of efficiency and productivity.
FAQ’s
- Does one use coolants with carbide inserts?
Depending on the nature of high-speed machining with carbide tools, either a lighter water-based coolant or a heavier oil-based one is essential.
- What is the main use of coolant in carbide tools?
Coolants provide direct cooling i.e lower the temperature of the tools and the work piece to ensure safety and smooth running of the processes.
- What is the concentration of coolant in machining?
Water-soluble coolants usually consist of one part each of water and concentrate. Depending on the need the ideal coolant concentration is usually between 3% and 10%.
- Which coolant is used in drilling?
Different kinds of coolants such as soluble oil, sulphurized oil, mineral oil and lard oil are used, depending on the nature of the work.
- What coolant is used while working with cast iron?
While machining cast iron with carbide tools, coolants are generally not used.